Floor elevation inspection is an essential step to ensure the safety of a building and its occupants. This process allows for the early detection of structural damages or weaknesses, enabling timely reinforcement solutions to prevent potential accidents or costly consequences. Let’s explore this together with A Chau!
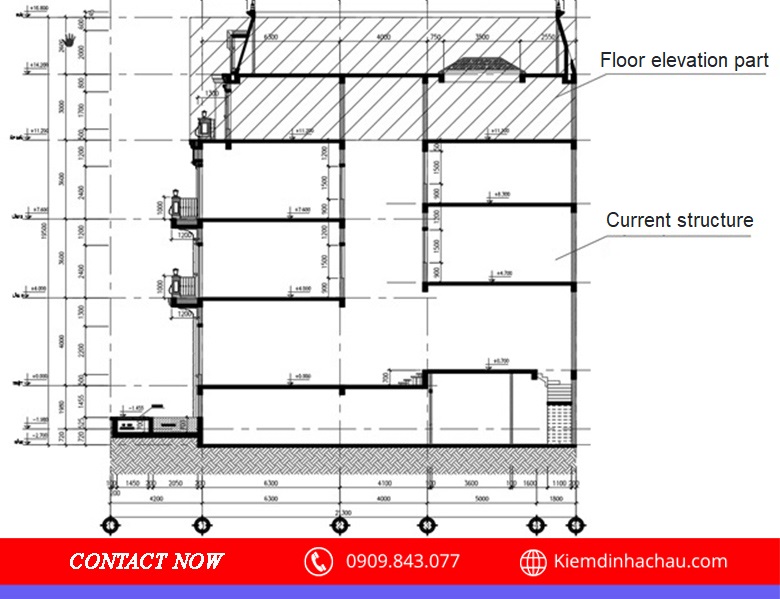
1. What is floor elevation inspection?
Floor elevation inspection involves surveying, monitoring, and conducting detailed testing of structural components and parts of a building, such as the foundation, pillars, beams, and floors, etc.
This activity aims to comprehensively assess the current quality of the construction, providing accurate evaluations of its load-bearing capacity and necessary reinforcement solutions before proceeding with the floor elevation process.
2. Cost of floor elevation inspection
The cost of quality inspection for a building is an important factor to consider during construction and utilization. This cost is not fixed and depends on various factors. Below are some key elements that influence the inspection cost:
Residential buildings: Houses, apartments, villas, etc., typically have lower inspection costs compared to industrial buildings.
Industrial buildings: Factories, enterprises, bridges, and roads often have larger scales and more complex structures, leading to higher inspection costs.
Infrastructure projects: Bridges, roads, tunnels, etc., require higher technical standards, resulting in increased inspection costs.
To give you an overview, here is a reference table of average inspection costs for building quality on the market.
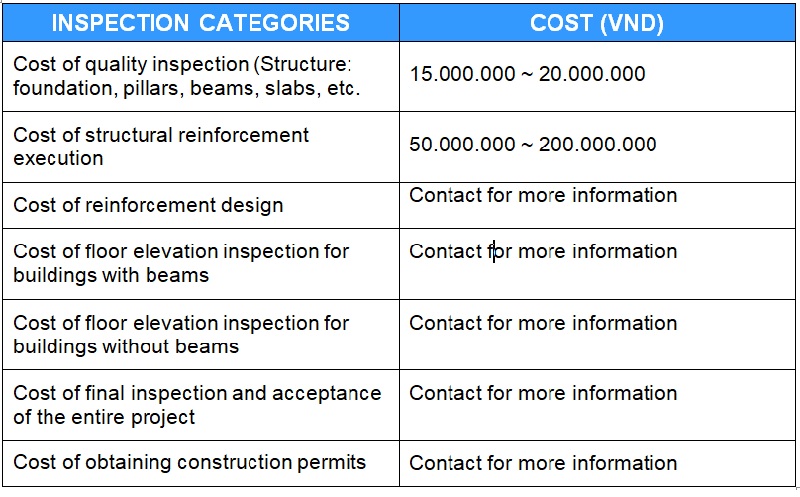
To get more information, please directly contact A Chau for advice and the most accurate cost estimate.
3.Important Notes When Performing a Floor Addition Inspection:
Based on practical experience, Asia Quality Control shares some important notes when conducting a floor addition inspection:
- Avoid being subjective about the quality of the foundation and the building due to a lack of expertise. It is necessary to thoroughly check the quality of the foundation, pillar concrete, and other factors of the existing structure before construction begins.
- Take advantage of the natural load-bearing capacity of the soil, as the soil's bearing capacity increases over time, which can help reduce the foundation costs for the floor elevation.
- Consult with construction experts to accurately assess the load-bearing capacity of the soil in the construction area.
- The process of drilling and inserting steel directly affects the load-bearing capacity after the floor elevation, so it is essential to choose a reputable contractor with experience in steel reinforcement to ensure the quality of the construction.
- Closely monitor the steel reinforcement process (oil mixture, length, surface cleaning, etc.) to ensure that no mistakes occur.
- Performing the floor elevation without permission is a violation of the law and may result in penalties. Therefore, it is essential to fully comply with the regulations regarding building permit procedures before starting construction.
- Choose a reputable contractor with extensive experience in floor elevation construction to ensure the quality and safety of the project. Be sure to thoroughly investigate the contractor's capabilities and reputation before signing the construction contract.
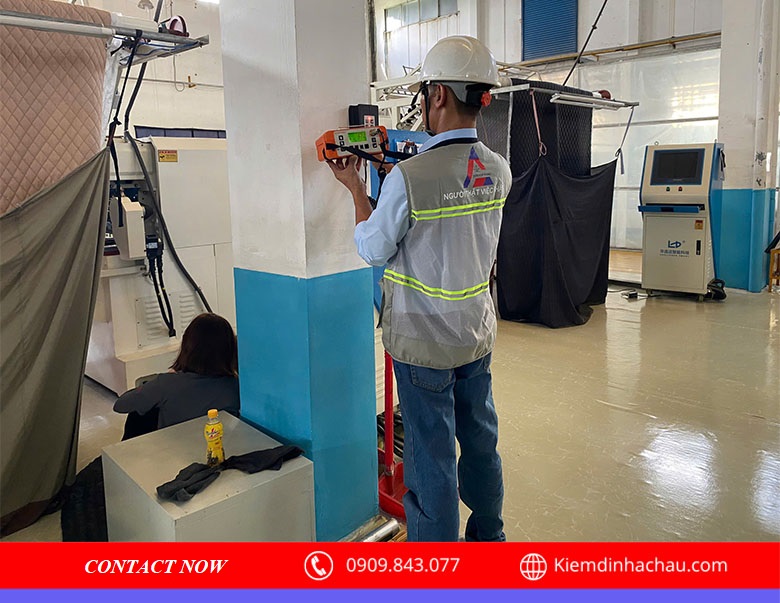
In addition, you should consult with inspection experts to get an accurate assessment of the building's condition and determine the appropriate solution for the floor elevation.
4. Standards and methods for floor elevation inspection
General standards as regulated:
The inspection of the floor elevation quality is a process that requires strict adherence to legal regulations and technical standards. In Vietnam, these activities must be based on legal documents such as the Construction Law No. 50/2014/QH13 and the Law on Amendments and Supplements to the Construction Law No. 62/2020/QH14.
In addition, national technical standards play a crucial role in evaluating the construction quality. These standards include:
- TCVN 2737-2023: Load and Impact - Design standards
- TCVN 5573-2011: Masonry and reinforced masonry structures - Design standards
- TCVN 5574-2018: Concrete and reinforced concrete structures - Design standards
- TCVN 5575-2012: Steel structures - Design standards
- TCVN 9381-2012: Guidelines for assessing structural damage
- TCVN 9343-2012: Concrete and reinforced concrete structures - Maintenance guidelines
- TCVN 9362-2012: Design standards for foundations and buildings
- TCVN 9379-2012: Construction and foundation structures - Basic principles for calculations
- TCVN 10304-2014: Pile foundations - Design tandards
- TCVN 239-2006: Dense concrete - Guidelines for assessing concrete strength in building structures
- TCVN 9348-2012: Reinforced concrete - Testing the corrosion of reinforcement - Electrochemical methods
- TCVN 9356-2012: Reinforced concrete structures - Electromagnetic methods to determine the thickness of concrete cover, reinforcement position, and diameter
The comprehensive and consistent application of these standards ensures the accurate evaluation of the load-bearing capacity of a structure during a floor elevation, guaranteeing safety and long-term durability.
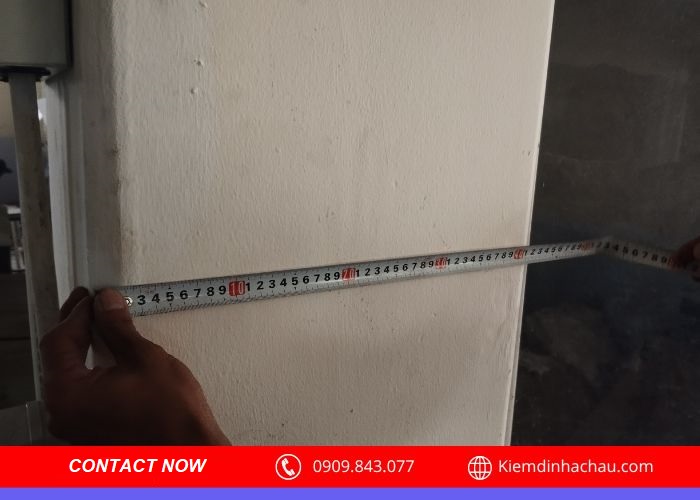
A Chau’s specific standards
A Chau always prioritizes quality in every inspection activity. Our inspection processes are built on three core values:
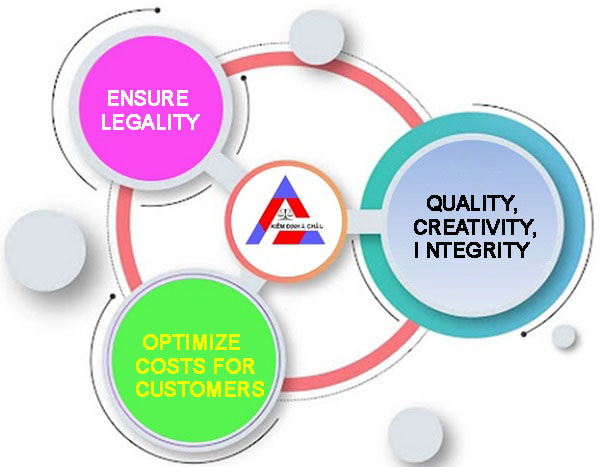
- Quality: Our inspection reports are detailed and clear, providing customers with an accurate and complete understanding of the actual condition of the construction, helping them make informed decisions.
- Creativity: We continuously research and apply new methods and tools to optimize the process, reduce time, and lower costs for our clients.
- Integrity: All surveying, testing, calculations, and evaluations are carried out objectively and honestly. We are committed to providing our customers with accurate and reliable results.
In addition, we always aim to optimize costs for our clients. We offer a variety of flexible service packages tailored to meet the needs and financial capabilities of each client, ensuring the highest efficiency for every construction project.
5. Content of floor elevation inspection work:
The inspection process is a thorough evaluation of the quality and safety of the construction. This process includes several stages, with the main tasks as follows:
- Site investigation: Engineers will conduct a detailed survey of the architectural layout and structural components of the building, noting any damages, cracks, or broken elements using visual inspection combined with manual measurements. Precise measurements of the dimensions of load-bearing components will also be carried out to collect enough data for calculation and evaluation.
- Sample testing: To assess the quality of construction materials, samples of concrete, steel reinforcement, bricks, and mortar will be collected for testing. Two main testing methods are used: destructive and non-destructive testing. Each method has its own advantages and applications.
- Deformation Testing: In addition to visual inspection, engineers use specialized measuring equipment to check the verticality of columns, overall building tilt, and deflection of beams and slabs. This helps evaluate the load-bearing capacity and stability of the structure.
Through these tasks, we can objectively assess the actual condition of the construction and then draw conclusions and propose appropriate technical solutions.

If you are planning to conduct the floor elevation to your house or other buildings, please contact A Chau for professional and reputable floor elevation inspection consultation and support.
For more related services of A Chau:
• Construction project quality inspection
• Factory inspection
• Construction supervision
• Factory design
• Vertification of design
• Structural reinforcement
ID POST: OFF365